Undergraduate research involving a transfemoral prosthesis at Georgia Tech.
In the summer of 2016, I conducted undergraduate research assisting with the design and evaluation of a dual-actuated transfemoral (above-the-knee) prosthesis. This research included the design of two different prosthetic foot designs as well as studying the human metabolic cost of transport for flat-foot and multi-contact walking. At the end of the summer, I presented this research at the S.U.R.E Research Symposium and won “Best Overall Presentation”.
1. Prosthetic foot design to allow for multi-contact walking
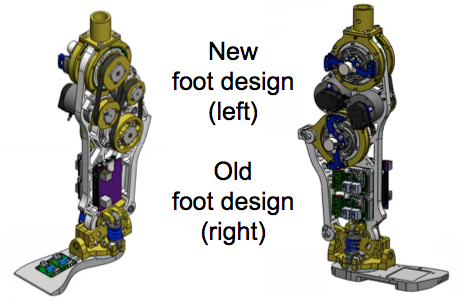
The first prosthetic foot I designed aimed to enable multi-contact 3D prosthetic walking. There were three primary design changes.
1. Side Profile
The profile of the new design is shaped in a way that will allow for toe/ground contact throughout the toe-roll during push-off. This enables for a higher torque push off and thus has the potential to decrease metabolic cost. The new design can be seen in the top image, the old design can be seen in the bottom image.
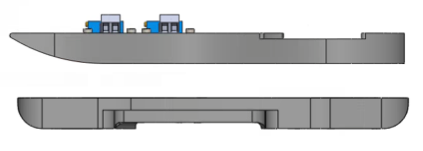
2. Top Profile
The contoured shape of the new design allows the foot to be placed inside of a sneaker. The new design also includes features to secure the force sensor voltage converter boards.The new design can be seen in the top image, the old design can be seen in the bottom image.

3. Force Sensor Mounting Features
The bottom of the new design includes features to mount flat force sensors. These force sensors allow the prosthetic to sense which phase of the gait it is in (stance verse swing). The new design can be seen in the top image, the old design can be seen in the bottom image.
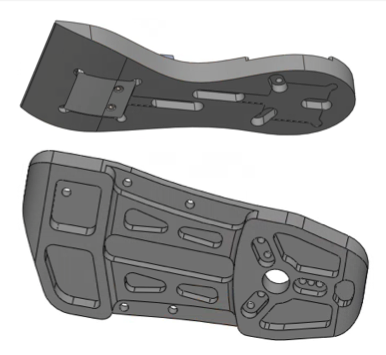
Machining
In order to machine the new prosthetic foot I became certified to use the Georgia Tech Machining mall.
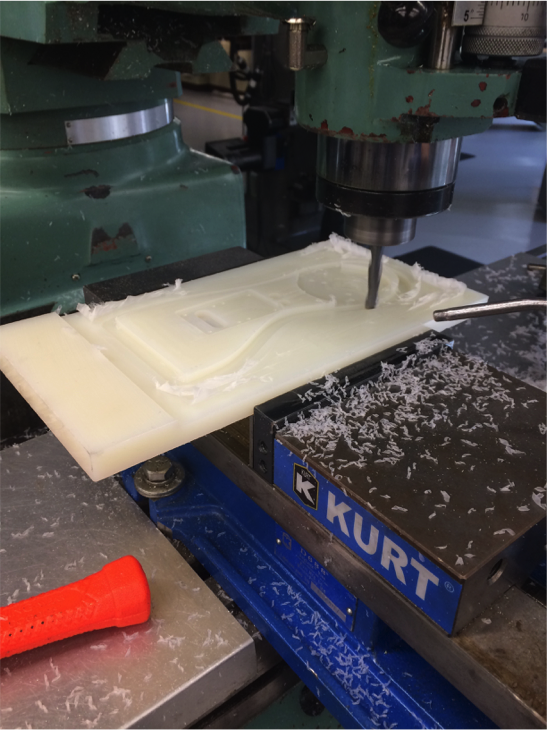
2. Prosthetic foot design to allow for energy capture throughout the walking gait
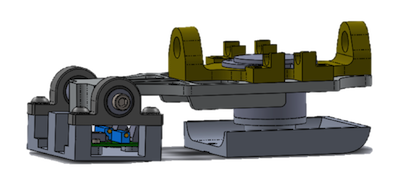
A second design was created to enable energy to be captured during the heel strike phase of the walking gait and then transfered into energy during toe push off. The design objectives for this new foot were the following:
- Low profile to avoid adding height to AMPRO3
- Use of a spring to add compliance and to capture energy
- A toe that can pivot to maintain contact with the ground during the "push-off” phase of the walking gait
- Designs that are easy to manufacture and low cost
- Curved heel to assist in the heel contact phase of the walking gait
3. Human Metabolic Cost Expenditure Experiment
To compare the cost of transportation for different forms of prosthetic walking (flat-foot versus multi-contact) I designed and ran a preliminary human metabolic expenditure experiment.
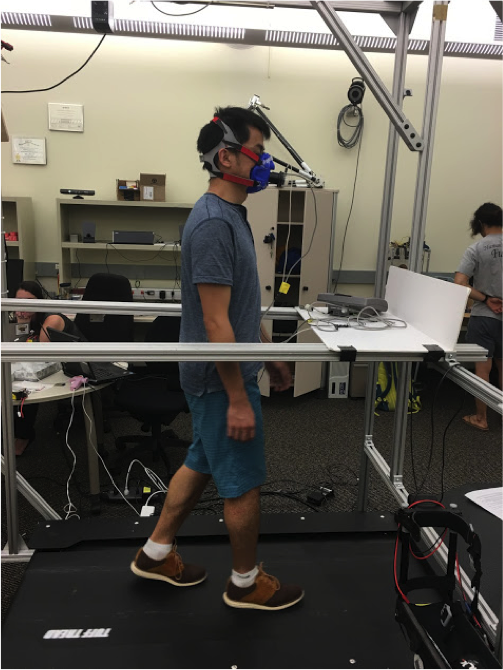
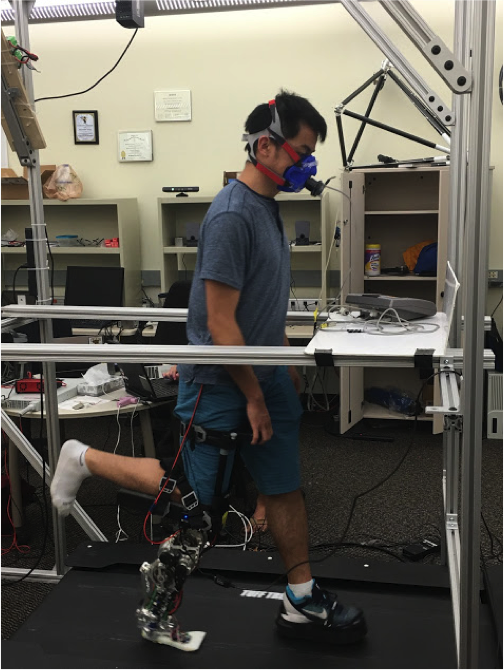
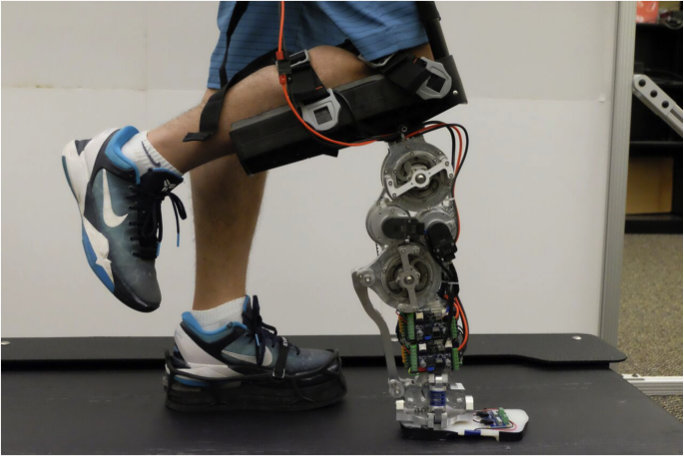
The results of the preliminary experiment can be seen below. The data indicates that the gate controller for multi-contact walking is not yet optimized due to it’s decreased performance compared to flat foot walking. The data is not representative of subjects with an amputation either since the test subject was able-bodied using a bi-pass.
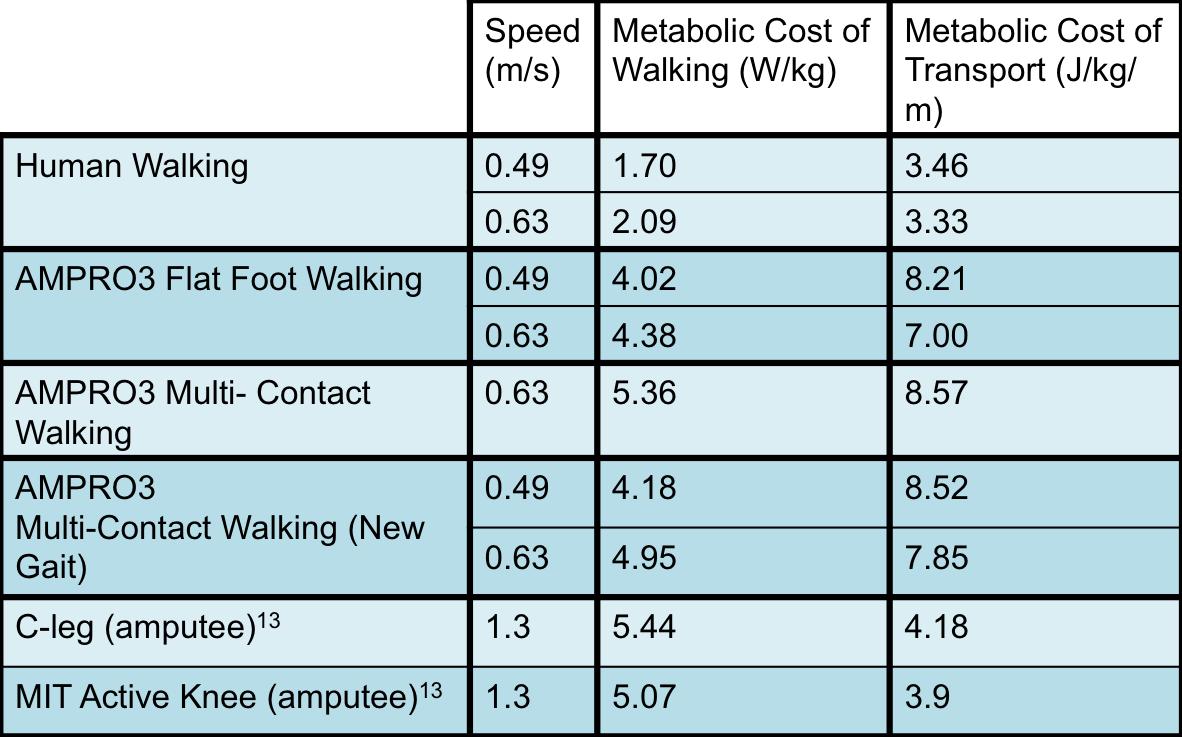
S.U.R.E Research Symposium
At the end of the summer, I gave both a poster and oral presentation showcasing my research progress made as a part of the Summer Undergraduate Research Experience (S.U.R.E.). This summer research program was a paid reserach position funded by sponsers including Intel and NSF. Among all 40 people that participated in the summer research program I won 1st place for “Best Overall Presentation”. Images from the event can be seen below.
My poster on “Evaluating the mechanical design of a transfemoral powered prosthesis through metabolic cost” can be seen HERE